https://www.kitech.re.kr/webzine/view.php?m=04&idx=473
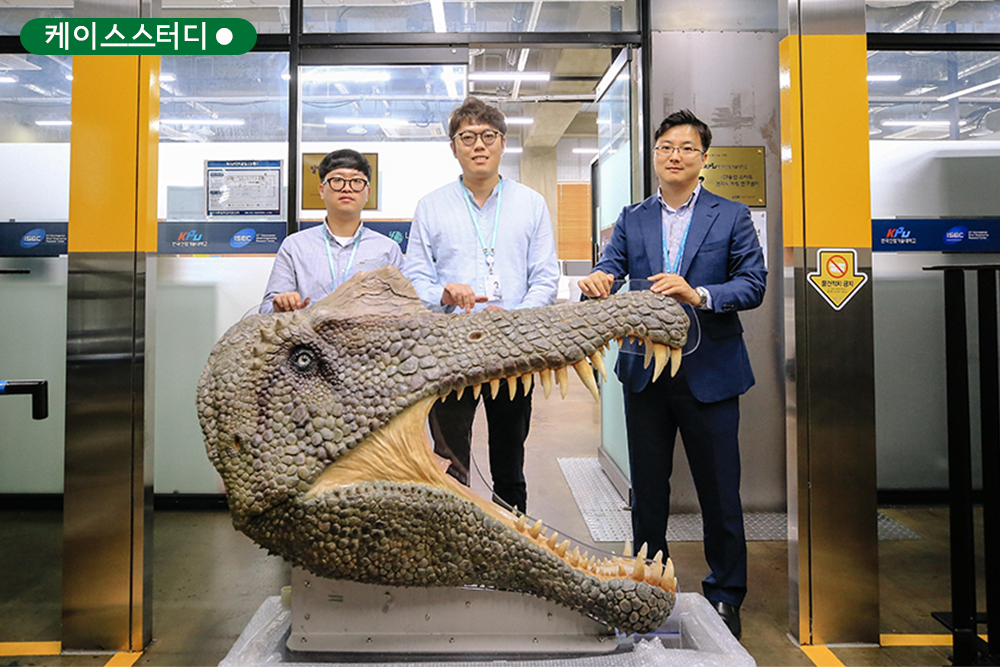
3D프린팅으로 만든 공룡 모형. ⓒ한국생산기술연구원
“글이나 사진 파일을 펴놓고 ‘인쇄’ 버튼을 누르면 종이에 똑같이 그려내듯이 3차원(3D) 프린터는 특정 소프트웨어로 그린 3차원 설계도를 보고 입체적인 물건을 인쇄한다. 놀랍게도 이 진기한 기계는 이미 서른 살이 훨씬 넘었다. 1980년대 초반, 미국 3D시스템즈사는 플라스틱 액체를 굳혀 물건을 만드는 프린터를 세계 최초로 개발했다.”
-물건을 인쇄한다? (물리산책, 이정아, 과학동아)
3D프린팅하면 일반인들은 교육용 교구로 만들어낸 캐릭터 장난감 정도만 떠올리게 된다. 하지만 생각보다 많은 분야에서 3D프린팅 활용이 가능하다. 시제품을 만들거나 인공관절, 인공장기 같은 정밀한 분야에서도 활용될 수 있다. 안경, 자전거 안장 등 비교적 크기가 작은 완제품부터 이제는 자동차까지 만들 수 있는 시대가 됐다.
다양한 3D프린팅 방식 중 가장 역사가 오래된 SLA 방식(Stereo Lithography Apparatus)은 레진(Resin)이라 부르는 액상 형태의 광경화성수지에 UV레이저를 쏴서 한 번에 한 층씩 굳혀가는 적층형 조형 기법이다. 이 방식은 자동차 부품 같은 대형 파트를 한꺼번에 찍어낼 수 있다는 장점이 있다고 박지용 한국생산기술연구원 뿌리기술연구소 공정지능연구부문 박사는 설명한다.
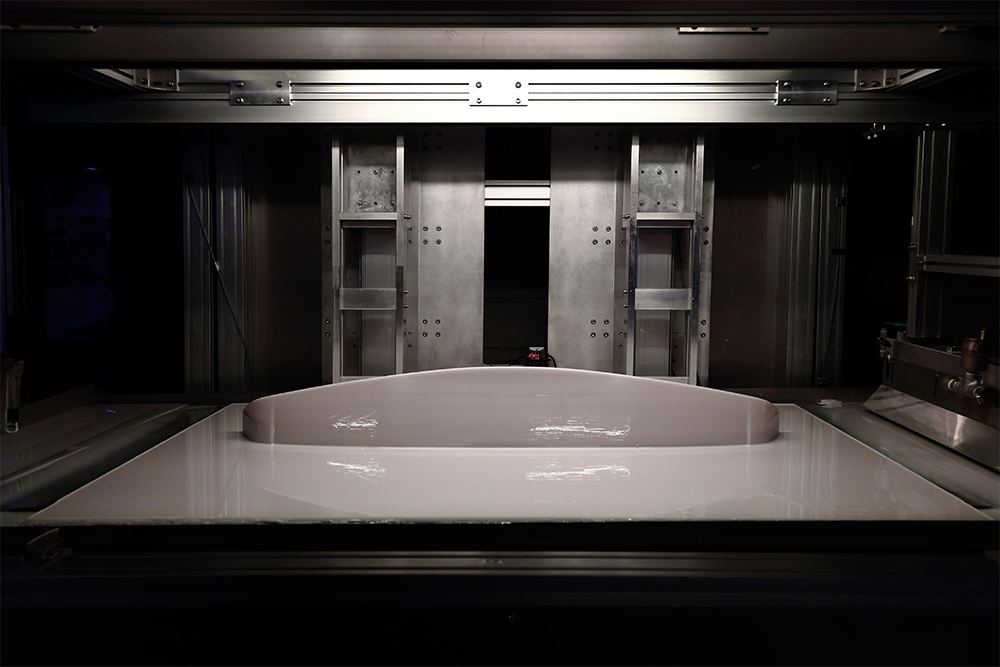
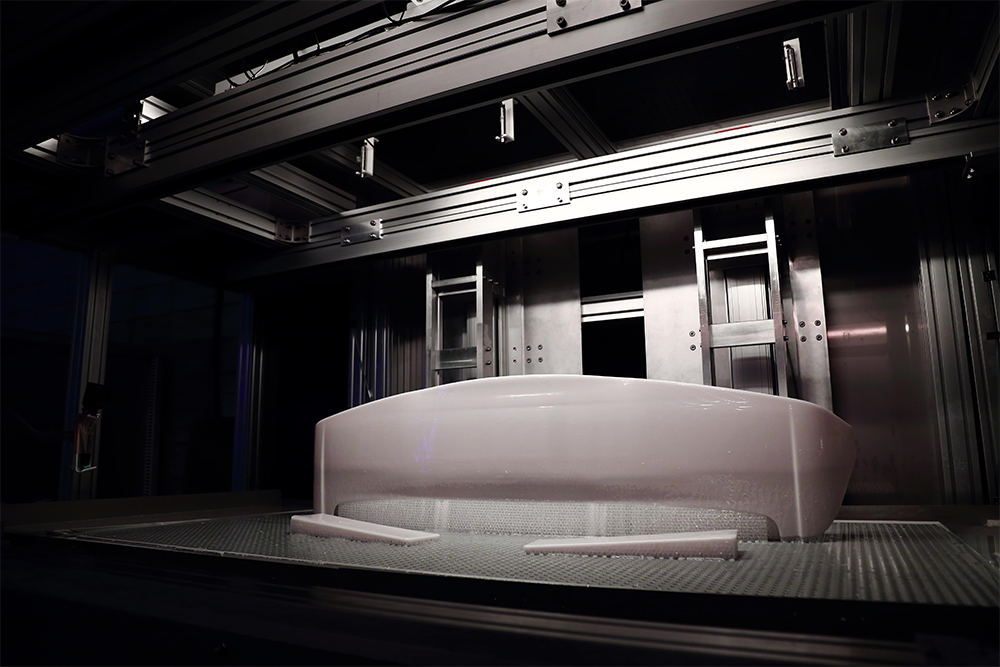
링크솔루션 대형 SLA 장비로 자동차 스포일러(Spoiler) 부품을 제작했다.
박 박사가 속해 있는 3D프린팅 제조혁신센터에서는 3D프린팅 공정을 하나의 체계적인 제조공정으로 발전시켜 설계, 생산, 실용화 등 기술서비스 전반을 제공하는 제조기반 구축 사업을 실시하고 있다. 한국생산기술연구원이 사업 주관을 맡고 대전·경남·전북TP가 참여중이다.
또한 실제 산업용 3D프린팅 장비를 구축해 다수의 기관과 기업들을 대상으로 시제품 부품 제조도 지원한다. 현재 국방부, LG, 현대, 두산, 아모레퍼시픽, 링크솔루션 등 다양한 기관·기업이 함께 하고 있다.
박 박사는 “자동차 부품 금형을 SLA로 만들어 사출을 통해 만들어낼 수도 있다. 최근 자동차 시장 트렌드가 다품종 소량생산으로 가고 있는 만큼 시장 트렌드에도 적합하다”고 전했다.
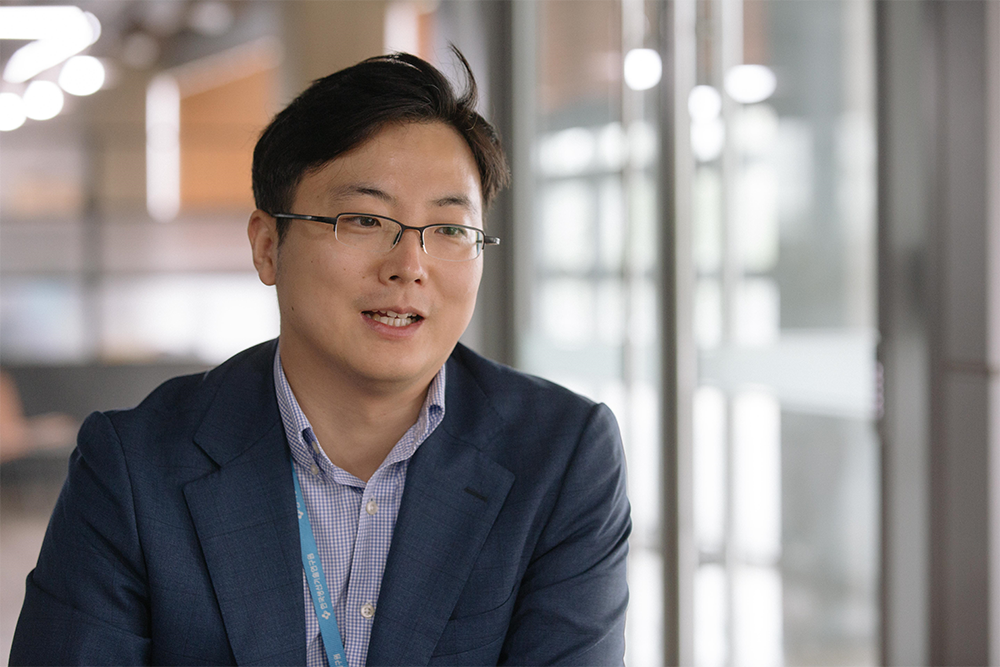
박지용 한국생산기술연구원 뿌리기술연구소 공정지능연구부문 선임연구원. ⓒ한국생산기술연구원
SLA 공정으로 만들어진 제품은 정밀하고 제작속도가 빠르며 표면 조도도 우수하다. 특히 아주 복잡하거나 섬세한 물건을 만드는 데 적합하다. 하지만 레진 가격이 높고 원료와 색상이 제한적인 것이 단점으로 꼽힌다.
만약 레진 비용을 절감할 수 있다면 SLA 3D프린팅 공정이 비싸다는 단점도 극복할 수 있게 된다. 3D프린팅 제조혁신센터에서는 3D프린팅 전문기업 링크솔루션에 이를 적용해 비용 절감 효과를 가시적으로 보여줬다.
링크솔루션은 3D프린터 개발 및 판매, 출력 서비스, 교육산업 및 컨설팅을 하는 중소기업으로 한국생산기술연구원의 기술지원을 받고 있다.
최근식 링크솔루션 대표는 “링크솔루션이 가장 잘하는 것은 크고 많이 빠르고 알뜰한 3D프린팅 기술인데, 그 중에서도 기존 운용비 대비 80%의 절감 효과를 낼 수 있었던 것은 한국생산기술연구원의 기술지원 덕분”이라고 말한다.
박지용 박사에 따르면, SLA 프린터에 레진을 가득 채우려면 1t 분량에 3~4억 원 가량의 비용이 드는데 레진을 15~20% 정도만 넣어도 가동 가능하도록 하는 기술을 링크솔루션과 함께 개발했고 이를 생산장비에 적용했다는 것이다.
특히 레진 1t을 다 채우더라도 1년 이상 오래되면 잔여물을 버려야 하는데, 이를 통해 고정비용을 크게 줄일 수 있다. 실제로 링크솔루션의 플로팅 레진 기술을 적용하면 레진 비용을 기존 약 3억 원에서 6천만 원 수준으로 80% 가량 절감 가능하다.
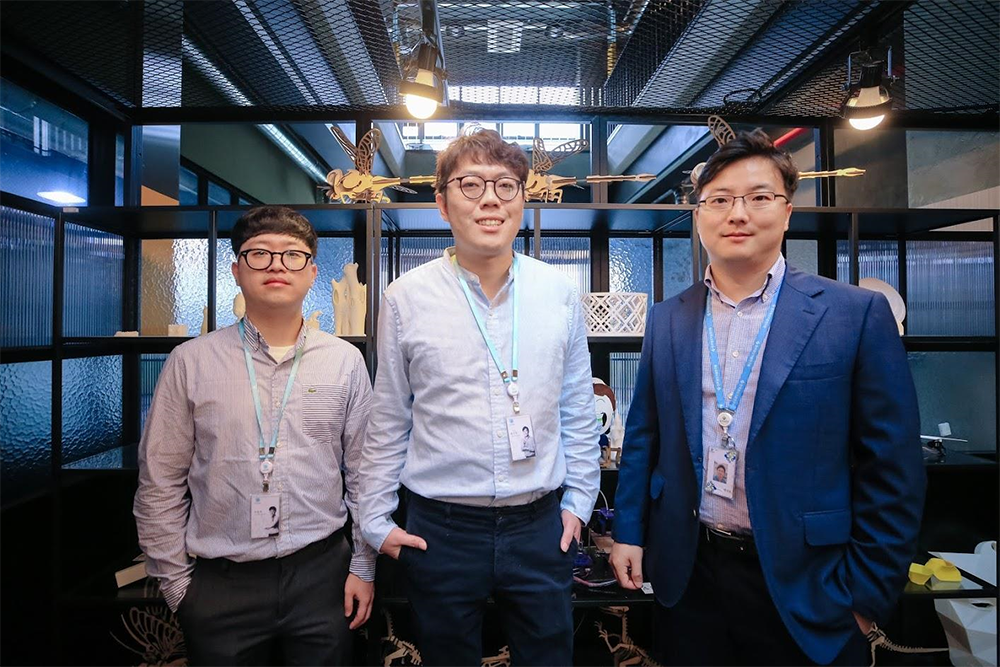
3D 프린팅 기술로 만든 제품들 앞에서 포즈를 취한 링크솔루션 최근식 대표(왼쪽 두 번째),
이강욱 개발팀장(왼쪽 첫 번째)과 박지용 선임 연구원(오른쪽). ⓒ한국생산기술연구원
이 같은 기술지원을 바탕으로 링크솔루션은 사업의 외연을 확장해 나가고 있다. 최근식 대표는 최근 “나나나(Me Me Me)세대로 불리는 2030 밀레니엄 세대가 주 소비층으로 등장해 개인의 취향을 존중하는 소비문화가 자리매김하는 가운데 식음료 및 의류는 물론 가전, 가구, 자동차 등 다양한 산업에서 ‘커스터마이징’ 제품 제작이 확산되고 있다. 3D프린팅 기술을 활용해 개인에게 커스터마이징된 제품을 보다 효율적으로 생산할 수 있다”고 밝혔다.
3D프린팅 금형몰드 생산, 자동차 맞춤형 대형 내외장 부품, LED마스크, 맞춤형 마스크팩, 대형가전 부품 생산 등을 통해 산업계에 새로운 제조 패러다임을 선사하는 것이 링크솔루션의 목표다.
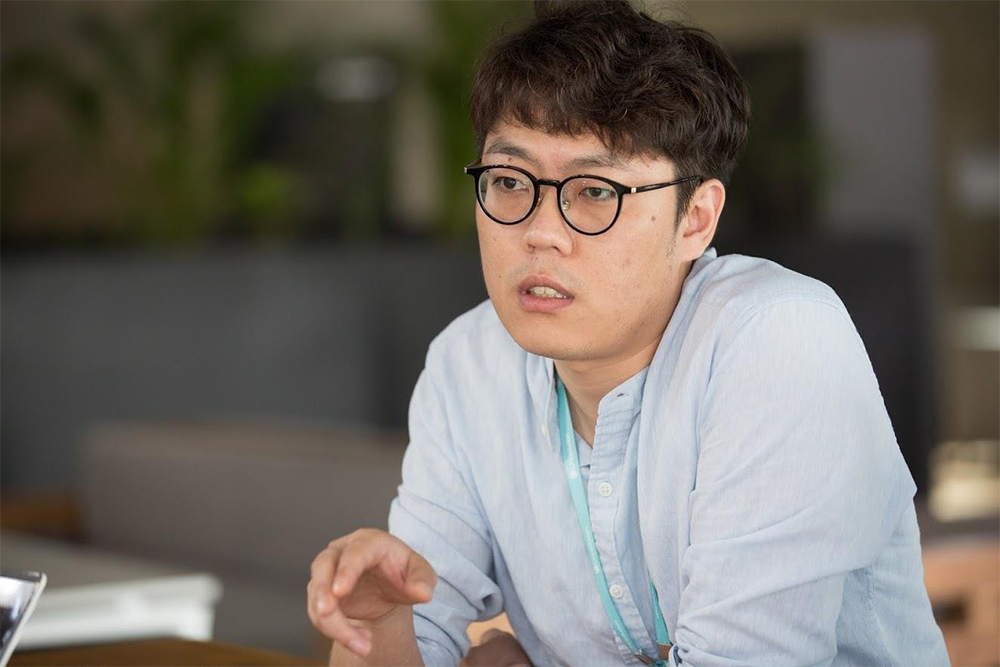
최근식 링크솔루션 대표. ⓒ한국생산기술연구원
맞춤형 마스크 팩의 경우 아모레퍼시픽, 링크솔루션, 그리고 3D프린팅 제조혁신센터가 협력해 세계 최초로 하이드로겔 마스크팩 3D 프린터 개발에 성공했다. 2020년 1월 세계 최대 전자제품 박람회인 CES에서 ‘2020 혁신 대상’을 수상했고, 2월에는 한국과 중국 서비스를 런칭해 5년간 독점 계약도 맺은 상태다.
또한 3D프린팅 제조혁신센터를 구심점으로 현대자동차, 덕양산업 등의 자동차 제조사들과 링크솔루션이 협력해 미래형 자동차의 그릴, 시트패드, 데쉬보드, 도어트림 등의 대형 시제품 파트들을 공동 개발 중에 있으며, 향후 실증을 통한 양산까지 계획하고 있다.
아울러 그 근간이 되는 3D프린팅 금형 기술 역시 현재 개발 중이다. 금형 분야는 5조 원 규모의 국내 시장이 형성돼 있어 3D 프린터가 이를 대체할 수 있다면 향후 발전가능성은 무궁무진하다는 게 최근식 대표의 생각이다.
최 대표는 “생기원과 함께 공정모니터링을 통해 기술을 업그레이드하고 품질과 생산성을 높여갈 계획이다. 생기원에서 그동안 기술지원뿐 아니라 관련 산업 분야와의 네트워크 형성에도 큰 도움을 줘서 감사하다”고 말했다.
TOP